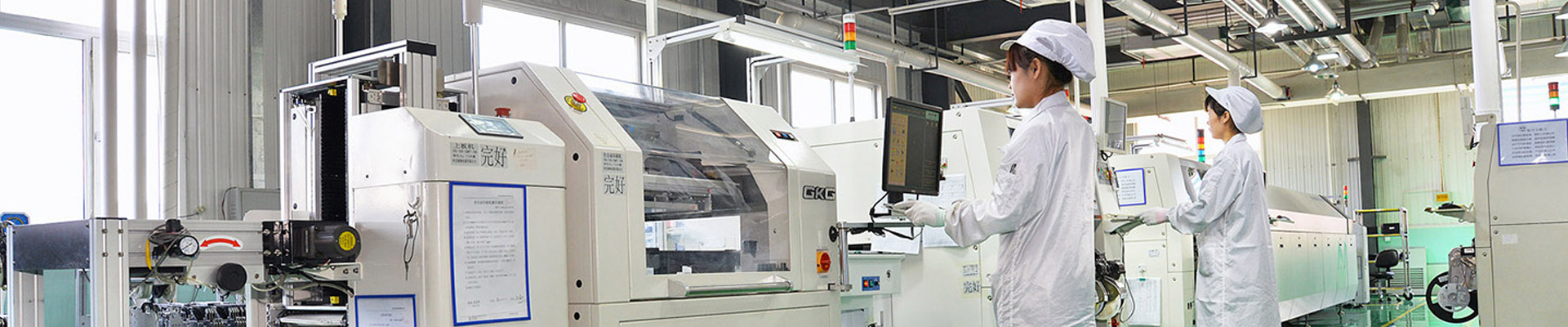
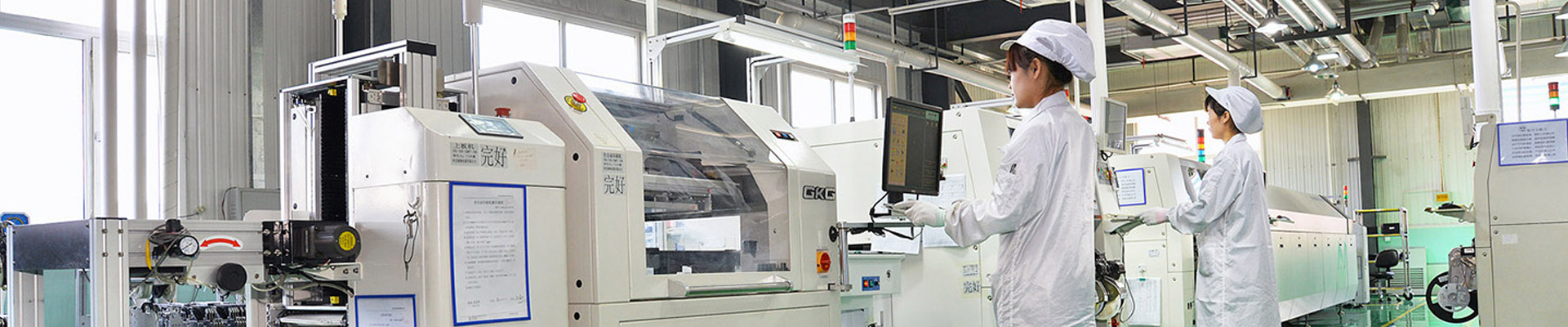
培训时间:2016年07月13日
培训地点:三楼多功能厅
培训主题:精益生产概论
培训内容:
精益生产概论
目录
• 增值与浪费
• 生产方式发展过程
• 理解精益生产
• TPS 的四条准则
• 如何实施精益生产
企业在做什么
• 实际上,我们唯一需要做的一件事就是研究从客户下单到我们收到款所需的时间,然后消除在这个过程中任何不增值的活动。
大野耐一(丰田生产方式TPS的创立者之一)
什么是浪费
• 任何不增值的活动
• 导致成本增加的因素
• 虽然增加价值,但耗用资源过高
•价值是与顾客的要求直接有关。
•有价值的活动:对我们而言,可以理解为加工、装配水泵、电机、绝缘检测仪等产品!!!
发现浪费和认识浪费的能力很重要
七大浪费
1.不良品浪费 2.过量生产浪费
3.搬运浪费 4.过分加工浪费
5.库存浪费 6.动作浪费
2.不平衡浪费
问题1
• 今天的培训是浪费吗?
一. 20世纪以前以欧洲(英法)为主导的单件生产方式
1. 产量低
2. 组织结构分散
3. 无标准化
4. 生产成本高
5. 劳动力在设计,机械加工及装配方面技巧娴熟
二、科学管理
1911年,泰勒发表《科学管理原理》(后更名为工业工程),标志工业工程的正式诞生。
1.强调科学管理,从而提高生产率;
2.创立了“时间研究”,改进了操作方法;
3.提出了一系列科学管理原理与方法。
三.福特的流水线
第一次世界大战后,由福特汽车公司的福特采用大量生产方式代替手工式单件生产方式, 以1908年福特生产的T型车为代表,1955年到达大量生产的全盛期。
1.统一计量
2.互换/简单,组装简便
3.劳动分工
4.需求量大
丰田生产方式
20世纪50年代,日本丰田开始摸索采用JIT生产方式,其鼻祖为丰田英二及大野耐一;新乡重夫的快速换模与防错起了至关重要的作用。
1.技术普及快/产品利润低
2.需求多样化/个性化
3.管理趋向人性化
1985年,麻省理工学院花500万美元成立“国际汽车计划”对丰田生产方式研究,由美国人丹尼尔、琼斯提出精益生产方式(Lean Productiong)概念。
TPS 的传播
• 大野耐一与一汽
• 新联工厂
• SVW 与 SGM
问题2
• 中国的工厂在哪个阶段?
从产生的背景看
精益生产(TPS)
=工业工程(IE)+戴明环(PDCA)+日本民族的敬业精神;是美国的工业工程在日本企业管理中的应用。
工业工程:是从事把人、原材料、设备作为一个整体去发挥其功能的科学;具有人机工程、动作时间研究、生产布局规划等等;源于泰勒,产生于美国;TWI(Training within Industry)是TPS一个很重要的基石。
戴明循环
PDCA的含义如下:P(PLAN)--计划;D(Do)--执行;C(CHECK)--检查;A(Action)--行动。
初期,P改为S(STANDARDIZE)--标准化SDCA。
最早由美国质量管理专家戴明提出来的,所以称为“戴明循环”。
是ISO9000与TS16949的基础。
5个为什么
1) 问题:某车间数控机床经常发生故障,维修人员通过更换备件解决故障
2)问题分析: 设备故障约每一个月发生一次,主要原因是主控制板发生故障,这种板的备件价格1,500元,每年备件费用18,000元。改善活动对主控制板故障的原因进行了分析,结果如下:
为什么发生故障 线路板烧坏
为什么线路板烧坏 降温不好
为什么降温不好 空气流通不畅
为什么空气流通不畅 数控机床外空气进不去
为什么空气进不去 滤网上结尘
通过追根究底地提问,找到了问题的症结,确认故障原因是:数控机床下面有一只滤网,是防灰尘的。灰尘积在滤网上使外面空气不能进入机床,从而使机床内空气散热不良,温度升高,造成线路板烧坏。
3)改善措施:每半个月清扫一次滤网
4)改善成果:备件每年节约10个,设备故障率下降83%.
问题3
• 到底什么是TPS?
由丰田公司半个多世纪的发展自然形成,从未写下来。
四条准则解释了TPS 隐含的内容,展示了其本质。
三条关于设计,说明丰田如何将其整个运营如实验一般的展开。
另一条关于改进,说明了丰田如何将科学的方法教授给公司。各个层面的员工。
准则1
• 准则1:所有工作都要详细的规定:内容、顺序、时间、以及结果。
• 在某个特定的顺序中,有特定的人去完成每项工作。
丰田的员工如何学习该准则:
教学互动
在工作的现场,问从事该工作的员工如下问题:
1. 你如何做这项工作? ?
2. 你怎么知道你做的是对的? ?
3. 你怎么知道结果是没有缺陷的? ?
4. 如果有问题怎么处理?
准则 2:个体如何互相联系起来
准则 2: 每个顾客-供应商的关系必须是标准化的,直接的;
发出要求与接到反馈必须是毫不含糊的(是与不是)的关系.
• 没有灰色地带; ;
• 第一时间寻求帮助; ;
• 对需求必须在一定的时间内有反馈。
准则 3: 生产线如何构造
准则 3: 每个产品与服务的路径必须简单并且明确详实的说明.
路径不得更改除非生产线进行了专门地重新设计过.
每次要用新的路径,必须要做实验.
产品与服务不是流向下一个可以获得的人或机器,而是特定的人或机器。
每个连向路径的供应商都是必须的,未连接的都是不必要的。
准则 4: 怎么改进
• 准则 4:任何改进必须基于科学的方法,由老师指引,并且在组织内尽可能低的层级展开。
• 一线员工对它自己的工作开展改进,而其主管作为老师,提供指导与协助。
丰田的理想状态
• 是否零缺陷(具备客户期望的特性与品质)?
• 能否一次完成一个需求的交付(批次的大小)?
• 能否按需要的版本供货?
• 能否立即交付?
• 能否毫无浪费地生产,如材料、人员,能源或其他资源(如与库存有关的费用)?
• 每个员工能否都在一个安全(物理地、情感地、专业地)的环境中工作?
精益生产的重要理念
现场现物现状(GO AND SEE FOR YOURSELF)
让问题暴露出来(SURFACE THE PROBLEM)
TPS与TS16949的关系
TPS是全球汽车业的最佳实践,所有人都在学,但无人超越;
ISO/TS16949是最早由国际汽车工作小组(IATF)制定,后来日本汽车制造协会(JAMA)也支持制定;
国际汽车工作组 International Automotive Task Force (IATF)包括如下9家整车厂:宝马(BMWGroup),克莱斯勒(ChryslerLLC),戴姆勒(DaimlerAG),菲亚特(FiatGroupAutomobiles),福特(FordMotorCompany),通用(GeneralMotorsCorporation),标致(PSAPeugeotCitroen),雷诺(Renault)和大众(VolkswagenAG)以及5个国家的监督机构:美国国际汽车监督局(
IAOB),意大利汽车制造商协会(ANFIA),法国车辆设备工业联盟(FIEV),英国汽车制造与贸易商协会(SMMT)和德国汽车工业协会-质量管理中心(VDA-QMC)组成TS16949=QS9000+VDA6.1,APQP来自与QS9000;后两者基础的理念、技术相似,但差异主要在于供应商与主机厂的协作关系。
版权所有 ©2016 河北深海电器有限公司 冀ICP备13019348号-1 网站建设:中企动力石家庄